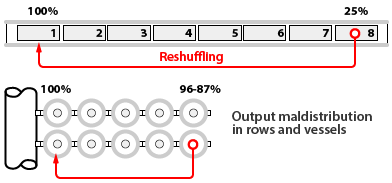
Complexity of operation and maintenance (O&M) of modern desalination plants cannot be reliably handled any more by long accumulated human experience, digital technologies shall be used. This article is an introduction into O&M automation principles.
Owners of desalination plants sometimes select services of O&M companies instead of hiring and training their own personal. And not without reason. The bigger the desalination plant is, the more complex the O&M services.
Today they may include not only maintenance of spare parts stock and equipment repairs, but the performance optimization. It addresses the seasonal seawater parameters variation (temperature, salinity, turbidity, etc.), the hourly electricity tariffs, and the reverse osmosis membranes performance degradation. It is due to "mileage" accelerated by fouling or scaling, or both.
Out of three optimization tasks, the RO membrane management (ROMM) is the most challenging. The reason is that nearly all the plant designers omit standby capacities for RO membranes turning them into the bottleneck of the plant O&M. Example is the IDE Technologies blog that states:
"The availability of the SWRO desalination plant depends almost entirely on the performance of its RO membranes..."
In a nutshell, well-thought ROMM framework shall handle two basic tasks - the membrane cleaning and the membrane elements reshuffling inside the pressure vessels.
The first task's timing and procedure – Cleaning-In-Place (CIP) - are well explained by the membrane manufacturers. Strong Indicators for CIP are decrease in the production and quality of the product, and increase in the pressure drop on the membranes. Ignoring these points may lead to irreversible damage of the membranes.
In practice this procedure is wrapped into the start/stop sequences of both SWRO high pressure pumps and CIP subsystems. (Warning: quick loading and unloading of the membranes – over 0.5 Bar/sec - may damage them too.)
These sequences are not automated by the plant designers, the excuse being its rare usage - normally 2 – 3 times per year.
Last 10 years some plants moved to advanced CIP schedule. Besides traditional infrequent "strong" and extended CIP, they practice "weak" and short CIP executed every 2 – 4 weeks. The latter makes ROMM resemble that of ultrafiltration systems. This schedule extends the useful life of the membranes by a factor of 2 or event more.
So ROMM requirement #1 is that the plant O&M shall be based on the advanced CIP schedule.
This schedule increases load on operators and the O&M expenses. To keep them at bay, full automation of start/stop sequences is required. The preferred time for such CIP is noon due to high noon electricity tariffs.
Transition to this ROMM requirement #2 cannot be done by O&M operator alone. It is not limited to re-writing the SCADA program, the hardware modifications are needed as well. Practically all the desalination plants do not tolerate frequent start/stops. Except for one – the Palmachim plant (Israel).
The CIP subsystems need re-designing as well, as in most cases they are not equipped with the on-line pH control, automatic chemical dosing, and cleaning fluid cooling. The same excuse.
The second part of advanced CIP schedule is the membranes reshuffling inside the pressure vessels. This task addresses the reverse osmosis phenomenon – decrease of the membrane production rate with the salinity rise. If the pressure vessel contains 8 consecutive elements, the output ratio between the first element and the last one may be well above 3.5. The membrane that works harder, ages faster. So reshuffling task is to even out the membranes "mileage".
In side-ported RO vessels arrangement output maldistribution between vessels exists as well but on a lesser scale.
So ROMM requirement #3 is real-time tracking of each and every membrane element mileage.
The seawater desalination plant of 100 MLD contains over 3000 SWRO membrane elements. Obviously this task cannot be done manually; software is needed. Can the commercial software for membrane performance projection (like ROSA) be used for this purpose? Not in the nearest future as they do not have standard API interface. It allows programmatic "conversation" with the core program instead of through visual interface.
More practical solution is merging all the mentioned software tools into one by applying reverse engineering. This is an approach selected by crenger.com.
Reverse engineering is an analysis of the product functionality with the aim to understand the product internal structure or code. Gained knowledge may be used to duplicate, enhance or develop the better version (in terms of customization) of the original product.
The better version – ROFlux calculator – is free for use. It handles membranes from different manufacturers and finds the average fouling factor and each membrane output needed for the mileage definition. It may be easily integrated into SCADA.
ROFlux clears the way to the last challenge – the membrane elements reshuffling. It produces tremendous volume of information. For example, if all 3000 elements are reshuffled, 3000 new positions are added to database.
The said procedure includes random testing and onsite autopsy of the membrane elements from different locations. The test results are used for the membrane end-of-life prediction and shall be stored in the same database.
So ROMM requirement #4 is database for storage of all the membrane runs and tests.
Crenger.com developed reference implementation of the described ROMM framework. This video shows the requirement #4 in action.