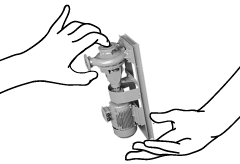
Recently I visited the 300 MLD desalination plant. What attracted my attention was a scrapyard adjacent to the plant. In rows were skids, membrane vessels, tanks, and piping pieces. The plant manager had no idea how to turn these wastes into profit. Internet is of no avail - the desalination industry with annual sales of over USD 26 billion (by 2025) has no websites for used equipment (UE) and parts resales.
How big is this market? For desalination industry alone, my educated guess is around USD 0.3 – 0.8 billion annually.
How to build such a website from scratch? Can we just clone one of the chemical equipment e-Billboards (pure advertising without internet purchasing) or do we need to start from eBay.com – the ultimate model of B2C eCommerce?
To start UE resales is not easy; some challenges exist. The first is building trust in UE quality control. It shall cover not only the UE manufacturing but the operation and maintenance history as well.
The second challenge is how to create a demand. The most probable consumer of UE is engineering services providers engaged in the projects' engineering and execution. They may admit reuse of the unwarranted UE provided that it is evaluated on the same basis as the new equipment purchasing. Without being part of this basis, the web application for UE resales will fail regardless of the price incentives. To communicate with the UE application the said basis shall be digital, hence it shall be crenger.com.
The UE resales plugin to the crenger.com platform includes two frameworks – the first is for quality control and history tracking, and the second is for technical specification.
Adding a new piece of equipment starts from uploading the collection of documents typically included into the Manufacturer's Record Book (MRB) of the equipment piece. It contains a number of sections: Acceptance, Materials & Fabrication, Inspection & Test Reports, and others.
MRB does not contain the equipment technical specification, it shall be submitted online. The UE plugin uses the simplified subset of Crenger.com specifications for new equipment types: valves, pumps, tanks and vessels, etc. This approach solves the interoperability issues between UE and new equipment specifications. The mentioned specification contains a number of questions concerning the equipment operation and maintenance history. The commercial part includes initial prices, warranty conditions, and depreciation parameters.
When the designer specifies the process or equipment, Crenger.com searches through available UE stocks and fetches only the best matches.
Shareable parts inventory
Spare parts Inventory (SPI) of desalination plant is rather expensive. It may reach $US 5 - 7 million for 100 MLD. The SPI size is a result of the plant design tradeoff between the plant availability and the spare parts delivery times. For example, the delivery time for a pump set is 15 - 50 weeks.
To decrease the SPI costs of maintenance, engineering companies normally strive to reuse the same equipment sizes in different projects.
This practice decreases the chances to win the project as it does not allow leveraging the economy of scale. Today most RO trains are built with 1000-odd m3/hour pumps, available sizes being as large as 3000 m3/hour.
How to move to more effective desalination without increasing the SPI size? By linking all the existing SPIs into a network - a virtual SPI.
The spare parts and items' exchange between SPIs may be in the form of resale or leasing.
Reverse Osmosis Membranes
An acquaintance of mine asked for my advice on extending the capacity of the reverse osmosis unit treating wastewater from a mine in South Africa. A quick glance at the operation data revealed an abnormality in every corner. It literally paralyzed my sound engineering judgement. Before officially accepting my defeat, I asked how profitable this unit was. Very profitable, the guy said, despite the fact that CIP (chemical cleaning) was done every 3 - 4 weeks, and after 4 months all the membranes were replaced.
If we made an assumption that the membrane costs might drop by a factor of 2 – 3, this abnormal design approach would revolutionize the whole Zero Liquid Discharge (ZLD) industry.
In search of cheap membranes we need not go far – just check the wastes of SWRO desalination plants. They treat the RO membranes as Consumables and replace them continuously. The plant's typical warranty sets the replacement rate at 3-4% annually. (For post-warranty operation replacement rates may be as high as 10 – 15%.)
As a result, there is a non-stop accumulation of end-of-life reverse osmosis membranes in landfills. According to IWA, the total capacity of SWRO plants is approaching 100,000 MLD. This figure allows us to assess that over 200,000 membranes are wasted every year.
To reuse them, we need to continuously track their operation history. Crenger offers a plugin that stores the membranes mileage, the membrane's locations after reshuffling, the results of the membrane autopsy and tests. Just watch this video.