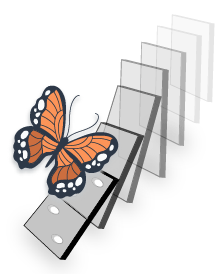
Project Engineering and Management (PEM) is intended to guide the company journey through the desalination mega-project stages: bidding, engineering, procurement, installation and commissioning.
Each stage is constrained by time, budget and quality. For example, bidding of 500 MLD desal plant takes 8 - 14 months, costs US$ 1 - 4 million and should be of the FEED-level quality.
These constraints explain the wide gap between modern PEM guidelines (pioneered in Oil & Gas and Pharma) and actual practices of the mega-project execution. They focus on removing the quality constraint and targeting the client's requirements as maximum, not minimum.
Even such a strategy does not substantially change the risk factor - every second project is not on schedule or budget. Out of nearly 40 companies eligible for mega-project bidding today, only about five managed to stay in business over 15 years.
For these companies the recipe for sustainability is to maintain the ratio between O&M and engineering services around 75:25. When designers are a minority, following PEM guidelines is not a priority. As a result bigger percentage of O&M leads to a loss of competitiveness, smaller one substantially increases the odds of bankruptcy. This golden ratio rule effectively blocks new companies' entry to desalination.
PEM itself fell prey to these constraints. The mentioned above gap between theory and practice questions PEM practicality. P&ID development, Safety Design (HAZOP), Reliability Design, Control Design, and Project scope definition are never done by the book. Piled up challenges block the PEM advancement to O&M - the final destination driver. Can one imagine the automotive industry without repair services feedback?
Can available software tools change the situation?
Except for 3D software dominating in mechanical design and accounting for roughly 20% of the project workload, all other tools are of questionable usefulness. To appeal to broader audience, they are kept as generic as possible. Generality inevitably leads to the tools' customization failure to catch the PEM specifics. Besides, covering the PEM space with disparate tools not complying with the information interoperability criteria creates data silos hampering against expectations the project execution.
How to start building software that will make modern PEM guidelines shine?
Two schools of thought dominate. They differ in starting point. The first one considers de facto ubiquity of 3D software as a green light (and safe grounds) to extending it to all other stages of the project. The second school believes digitization shall start from procurement contributing most to the project success.
Both approaches are non-holistic, and both failed to discover the information modeling law for sequential processes. It states that the longer the sequence, the higher the abstraction level of the first process is.
In other words, no project stage should be skipped: information modeling should start from process engineering and follow the engineering thinking. Higher levels of abstraction are, in fact, new fundamental knowledge.
The overturned pyramid below captures the PEM paradox - each next level up has higher weight in the project-plant life cycle, but its success depends on the previous one. (So the above-mentioned assertion that procurement contributes most to the project success is not entirely correct.)
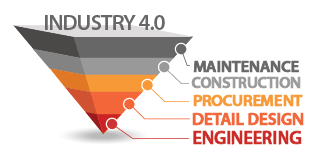
The best illustration of PEM paradox is Computerized Maintenance Management System (CMMS). Over 80% of its numerous implementations fail due to disconnect from previous layers. The same may be observed in commissioning and project scheduling software.
The following fact gives true indication of the layer weights. During commissioning AquaSure carried out over 200,000 tests on 28,500 pieces spending 70,000 man-hours (Victoria plant, Australia, 2012). It is over 2 times more than the plant 3D modelling or instrumentation and control design and execution.
These figures throw dim light on who gets credit for the project success against all odds. Today the project risks perception by stakeholders is a guesswork well described by the parable of the blind men and an elephant. To move from perception to in-depth analysis, full project metrics is needed. As the management guru Peter Drucker famously said, “If you can't measure it, you can't improve it.”
Missed metrics is a vicious circle. Metrics defines the true north and a route of the PEM digitization, but to figure them out, PEM shall be digitized.
Can the vicious circle be broken? Crenger.com proves it can. Holistic is the password.
Information modelling is a single point of entry into digitization.
Its success depends upon the P&ID and P&ID item abstractions - the first in a sequence. They trigger endless chain of changes in systems engineering (the butterfly - domino effect) and lay down the foundation for new P&ID development framework accelerating engineering by a factor of above 50. There is no upper limit as scaling the plant design may be done automatically without the project engineer help.
The other fundamental abstractions are Selector, Serial, Function, Event, Task, Business, Product, etc. They make transition to project management seamless: project scheduling, costs estimation, and metrics are automatically derived from engineering database. Metrics covers 3 entities: materials and equipment pieces, resources usage, and project evolution.
Project evolution management is what comes after project change management. It is by far the biggest component intended to build virtual circle of know-how mining. It focuses on how we do what we intend to do. It is a true business purpose of the PEM digitization.
With 10X speed projects are not the purpose anymore.