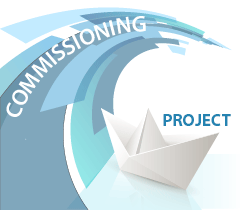
Commissioning brings logic and purpose into a collection of equipment and piping pieces. It shall demonstrate to the client that the plant complies completely with the functional requirements set. It is even more important to the contractor as it validates all the lean engineering practices, assumptions, and risks accepted during the process engineering and the equipment supplier's selection. Commissioning followed by the plant handover is a major value-adder to the engineering company's expertise. It may bond the relationships between the parties for good or break them forever.
The commissioning work scope is tremendous. An example is Victoria’s desalination plant (Australia, 2012, design capacity of 410 MLD). AquaSure – a company in charge of its commissioning - carried out over 200,000 tests on 28,500 pieces, spending over 70,000 man-hours.
Probably, your first reaction is that it cannot be true and that AquaSure cheated on a client. Not in the least. Below is an excerpt from the commissioning metrics of the 450 MLD SWRO desalination plant. It was auto-generated by crenger.com as part of the FEED package. Amazing coincidence, isn’t it?
Total number of checks and tests to be executed – 210509.
Total number of assembly and calibration certificates to be signed off and filled – 10240.
These figures suggest that the impact of commissioning on the project schedule and budget is heavy; its mitigation recipes are part of the plant contractor's know-how.
The commissioning package defining scope and resources shall be part of the project offer. Lack of it is a legitimate reason for disqualifying the bidder.
Commissioning is the best example of concurrent engineering in action.
Commissioning shall be carefully orchestrated from the beginning of the project. For example, the P&ID development shall answer the question of how the hydro-tests of piping and subsystems shall be executed. Frequent mistakes are forgetting to add blind flanges or isolation valves needed for hydro-tests, not providing room for high-precision torque meters for the pump performance tests, or spare parts and consumables for commissioning runs.
Commissioning is where the subsystems may and shall fail. "Do they fail safe?" is the most important test. "Fail-safe" design principles for subsystems shall be explained to the client. The lack of this is a firm reason for the contractor's disqualification.
The commissioning content and procedures are well documented in the industry. An excellent example is Norsok's Standard Common Requirements - Mechanical Completion & Commissioning.
What makes this document of 1996 outstanding is this sentence.
An electronic-based system for the administration of mechanical completion, commissioning, and punch list register, should be used.
The authors (with nearly zero computer literacy) saw no alternative to digital means of commissioning management due to the mind-blowing scope of the multidisciplinary work compounded by its inevitable outsourcing.
Today, 22 years later, no leading engineering company engaged in desalination projects implements this requirement in full. In other words, commissioning is a litmus paper differentiating the digitally minded contractor from the one still betting on Excel and Word programs.
What are the commissioning basic points?
Health and job safety. NAZOP study shall be completed prior to any activities in the field. The plant layout shall be marked up with the areas of potential hazards. A checklist of all required safety precautions including requirements for work permit shall be made. Crenger.com solves both tasks automatically. In addition, it notifies the stakeholders of the forthcoming equipment energizing.
Commissioning roadmap. It defines a work pack for each milestone and reflects the sequential and cumulative character of commissioning. The roadmap takes into account the subsystems' lead times, their interaction, and how the plant is divided into "fail-safe" modules. Two last points are an objective of the Commissioning Sequence of the plant auto-generated by Crenger.
Auxiliary subsystems like dosing or cooling ones shall be commissioned first – they may be needed during main subsystems commissioning.
The core of the work pack is the Inspection & Test Plan (ITP). It lists the activities to be executed on the subsystem under commissioning and those requiring witnessing. ITP is generic and valid for all the subsystems with the same prototype.
Crenger controls the commissioning flow; it creates the punch list which entries are anchored into P&ID, the plant layout, or wiring diagrams.
Mechanical connections check. It verifies that all the instrumentation, piping, and equipment pieces are connected according to P&ID.
Sounds simple, unless the number of pieces to check is really big – 11273 in the 450 MLD plant.
To greatly simplify this task, Crenger auto-generates the barcode for each element of P&ID which is to be pasted to the equipment piece before shipping or during the product quality control.
Equipment installation check. It mainly addresses rotating equipment – mixers, scrapers, pumps, and motors. Crenger auto-generates Alignment Certificates and Installation/Assembly Certificates of Compliance (COC) forms filled with proper data (web or Excel forms).
Electrical connections check. It includes power, instrument and control cables, earthling, and grounding. Crenger auto-generates Assembly Certificates for all connections. For the 450 MLD plant their count reaches 7000.
Piping flushing and hydro-tests. The time-consuming part of the hydro-test is to compare the design pressures of the elements installed on the piping and find the weakest link. Crenger automates this process and generates the hydraulic test forms filled with proper information.
Instruments and loops calibration. Crenger auto-generates the certificates with reference documents list, the process data, and excerpts from P&ID and layout location.
Control & Safety logic dry test. Crenger generates the list of loops, alarms, and interlocks for each subsystem.
Equipment functional test. Often failure to execute the functional test is explained by the lack of high-precision instrumentation, incorrect installation of instrumentation, and far-from-ideal testing conditions requested by the proper international standards. These points shall be reflected in the P&ID and conveyed to clients as early as possible.