Times are gone when the pump selection was boiled down to the definition of the head, flow rate and material of construction. Nowadays high-capacity high-head pumps for desalination applications are a sophisticated piece of equipment always custom-tailored to the client requests. These pumps are a critical path component of the project schedule and the major contributor to the overall energy consumption of the plant.
Below is an overview of key points that may help you in deciding which pump is right for you, and may enhance the performance and reliability of your pump at no cost.
Pump efficiencies
Term "pump efficiency" unconditionally means only the HI (Hydraulic Institute) level A no-minus tolerance pump efficiency measured at the pump discharge nozzle.
Now it became obvious to all pump manufacturers that seawater desalination requires better efficiencies than those witnessed in the API pumps intended for the chemical industry or the power one.
Life-cycle cost analysis shows that 1% gain in the pump efficiency in the BOO project produces net revenue roughly equal half the pump price! Efficiencies prediction at the bidding stage is a crucial factor in winning the competition. I know of a case where the bidder was awarded the order for EPC project mainly because his/her efficiency estimate was only 2% better!
In predicting pump efficiencies the following points should be taken into account.
- Not all major pump manufacturers have enough expertise to engineer and manufacture high-efficiency pump.
- The pump manufacturers quote efficiencies that are 0.2 - 1.0%! (abs) less than the ones demonstrated during the performance tests. As a rule such pumps are slight modifications of some base design already having good operating records.
- The best efficiency point location is very difficult to predict. Event for the same batch of the pumps the dispersion of BEP may be on the level of 10%!
- Site efficiencies are 0.5 - 1.5% less then those demonstrated during the performance test at the manufacturer's test-bench. Main reasons are worse hydraulic conditions at the pump suction. Application of the stream stabilizer inserts may restore the pump efficiencies. It pays back quickly.
There are no other methods of improving efficiencies than the impeller hydraulic passage optimization and impeller surface polishing. Ceramic casting as a way of efficiency improvement is no longer used due to high costs (except for Flowserve applying ceramic casting to impellers). Coating is best avoided for high pressure pumps.
The best way to measure the pump efficiencies during the acceptance test is with the torque meter.
The efficiency degradation over time shall be taken into account when specifying the motor size.
Operation points for VSD-driven pumps
It is a standard practice now to define multiple operation points for variable speed pumps (SWRO and BWRO units) in the form given below.
Table 1 Pump operation point specification template
Point description | 1(clean membranes, low salinity, high temperature) | 2(low salinity) | 3(high salinity) | 4(fouled membranes, high salinity, low temperature) |
---|---|---|---|---|
Head, m | … | … | … | … |
Flow rate, m3/h | … | … | … | … |
… | … | … | … | … |
Load duration,% | 10 | 40 | 40 | 10 |
Point is used for | Pump size selection | Guaranteed performance | Guaranteed performance | Motor selection only |
Table 1 should be accompanied by description of the BEP desirable location. It is not rare that the guaranteed performance is requested for more than 2-3 points.
Another typical example of the multiple operation points is the intake pumping station. Its design should include some procedure of intake and delivery piping cleaning and be always checked against piping clean and fouled conditions.
Given the operation points, load duration curve, performance curves, the seawater temperature variation, the pump average efficiency is defined by integrating the actual power consumption over the time of the year.
Any case of VSD-driven pump shall be thoroughly analyzed to justify the VSD application. The reason is that the VSD efficiency drops substantially at the partial loads; at 30 - 40% load the expected VSD efficiency may be as low as 88-90%. The partial-load combined VSD and AC motor efficiencies are best represented by the following table. It should be requested from the VSD manufacturer.
Table 2 Combined VSD + motor efficiencies
Load | 20% | 40% | 60% | 80% | 100% |
---|---|---|---|---|---|
20Hz | ... | ... | ... | ... | ... |
30Hz | ... | ... | ... | ... | ... |
40Hz | ... | ... | ... | ... | ... |
50Hz | ... | ... | ... | ... | ... |
60Hz | ... | ... | ... | ... | 98% |
Pump size
Pumps fit well the economies of scales: bigger pumps of the same design have higher efficiencies. On the other hand the specific cost of the pump per m3/h of water drops substantially with the size. So from the client perspective the bigger pump the better.
As follows from the table below for high pressure service (50 - 60 Bar heads) the current pump market cannot offer a meaningful variety of options.
Table 3 Pump size demand
High-head pump flow rate, m3/h | 1200-1400 | 2200 -2400 | 3200-3400 | >3600 |
---|---|---|---|---|
Qualified bidders | 8 | 3 | 1 | 0 |
Quality assurance complexity (author estimate) | 1 | 5 | 10 | 10 |
Startup and shutdown complexity (author estimate) | 1 | 2 | 4 | 4 |
Table 3 figures reflect the fact that most of the desalination plants have been built around the 1000 - 1500 m3/h capacities. Three factors mostly define the optimal size of the pump.
- the plant total capacity,
- the plant operating load curve,
- the reliability of the SWRO membrane array connected to the pump - weakest element in the chain of equipment pieces.
Given the steady growth of the plant capacities, tendency to capitalize on the low night tariffs for electricity and substantial increase in the reliability of the SWRO membranes, their vessels, valves and permeate discharge connections, it may be said that the 2000 - 2500 m3/h capacities will be dominant in the next 10 years to come.
Pump history
A pump with good operating records is a first candidate for selection provided all other requirements of the client specification are met. Most important document in the pump "resume" folder is the reference list including the information about the construction materials, fluid parameters, rotation speed, batch size, a company name bought the pump and a date of the pump commissioning. If this pump make has been used in your company projects in the past, summary of the pump performance test results, PREN of materials used (from Certificates of Material Compliance), and any problems encountered during pump manufacturing (mainly, casting), commissioning and operation shall be added.
Less clear situation is when the bidder comes up with a pump that is a modification of the existing pump or a new pump having a prototype differing in a type of service (for instance - refineries), materials, fluid type, pressures and temperatures. In such cases the prototype analysis shall say whether we can expect the same good performance and - most important - reliability from the pump scale-up.
Table 4 below shows worst case scenario - hydraulic performance scale-up recently submitted by the pump manufacturer for one of the projects. It requires engineering the pump from scratch. Worst, apparently sloppy selection of the prototype dents a hole in a company reputation (that has more influence on customer loyalty than its brand image).
Table 4 Pump hydraulic scale-up example
Pump | Flow, m3/h | Head, m | Rpm | Driver, kW |
---|---|---|---|---|
Prototype | 750 | 65 | 980 | 320 |
Offered pump | 2200 | 620 | 2980 | 4000 |
Vicarious experience (gained from talks with the pump manufactures and designers) and my own one of new pump risk analysis may be condensed to the following simple rule of thumb.
The new pump is acceptable if and only if its prototype is designed for the same range of operating pressures and flow rates differing from the new pump ones not more than 30%. This scale-up allows only minor modifications of the nozzles, impellers and case passages; external casing dimensions most probably will not be changed.
To get out of the vicious circle of new pump marketing, manufacturers may offer prices discounted by 30 - 50% against those for pumps with already proven good operating records. For EPC projects it may have sense to invest time into studying such offers in more depth.
First, the manufacturer should produce enough evidence to convince the client that
- the ordered pump is within the range of the pumps already manufactured in the past as regards the construction materials and the flow rates and pressures;
- the manufacturer already successfully managed such projects in the past - to build a pump from scratch and within the project time limits;
- the manufacturer pursues strategic goals going beyond the current order;
- the pump engineering is actually on.
Second, the client should add the following points to his or her project schedule.
- In-house pump engineering takes more time (from 2 to 3 months).
- All engineering reports including CFD analysis and natural-frequency (rotodynamic) one should be verified by the third party, (1 month to add).
- Machining of the pump casing should be done only for the first pump, followed by assembly and the performance test. If the test succeeds, manufacturing of other pumps is to be resumed. (3 months to add)
Construction materials
All available material choices for pumps working on seawater, brine and permeate lay within 2 families: austenitic/superaustenitic steels and duplex/superduplex ones.
Table 5 Pump materials
Groups | Cast specifications | Wrought specifications | PREN | Relative costs | Service |
---|---|---|---|---|---|
Austenitic steels | CF3M ASTM A351 | AISI 316L | 23 - 30 | 100 | permeate |
ASTM A182 | AISI 904L | 36 - 40 | 130 | Brackish water, BWRO stage reject | |
Specialized alloys | Alloy 885 (Flowserve pumps) | 38 - 41 | 160 | Seawater, brine | |
Duplex steels | ASTM A890 Grade 1A - 4A | UNS S32550 | 30 - 38 | 130 | Brackish water, BWRO stage reject |
Super duplex steels | ASTM A890 Grade 5A - 6A | UNS S32750, UNS S32760 | 40 - 46 | 160 | Seawater, brine |
PREN = Cr + 3.3Mo + 16N
To avoid pitting and crevice corrosion in superduplex steels at seawater high temperatures (above 30 degrees C) under biofouling films, pumps should be flushed with service water or drained after any stoppage.
In specifying construction materials the following should be taken into account.
- As the pump initial cost is about 5 - 7 % of the total life-cycle costs in heavy-duty applications, the material cost optimization is meaningless.
- For auxiliary seawater pumps with annual operation below 1000 hours AISI316L steel with cathodic protection may be considered.
- The pump manufacturer experience in seawater applications shall be studied. For example, placement of an order with the manufacture having no prior experience with superduplex is fraught with a risk of the casting low quality.
- Witnessed inspection of castings for big pumps before machining is mandatory.
Shown below is heavy corrosion in pumps made of duplex steel after 3 years of operation, most probable reason being defective casting of casings and impellers.
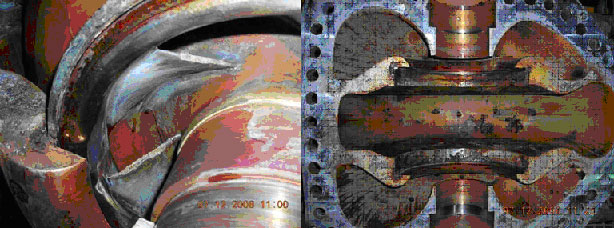
Pump design and construction
Two types of pumps for high-head high-flowrate service are available on the market: axially split and radially split ring-section pumps. Axially split pumps are more robust, heavier and more expensive (by approximately 20%). The ring- section pumps as a rule have higher efficiencies, shorter life and higher susceptibility to load change and seawater stagnant conditions (because of single-side impellers and hydraulic bearings). These pumps have capacity range below 1400 m3/h and are the best choice for seawater desalination units installed on the sea vessels with less than 5000 hours /year of operation.
Sleeve bearings with forced lubrication system may be reliably applied to the pumps bigger than 1250kW.
Surface hardening is recommended for wear rings, the shaft sleeves and packing glands
Negotiating price and terms
Not seldom negotiating prices is started without clear understanding of what is to be negotiated.
Generally negotiation package includes
- price,
- quality (including manufacturing facility and foundry location),
- guarantees,
- penalties for not meeting the guarantees,
- payment conditions and delivery time,
- after-sales services
The practice of aggressive price reduction - the lower the better - has its pitfall: current tough competition and low revenue margins in industry leave the manufacturer no other choice then to cut on quality assurance expenses. This serves neither manufacturer nor user. I witnessed a case where a very reputable manufacturer without prior notice to the client handed over machining of casings to inexperienced subcontractor. As a result four out of nine 5000 kW pumps had defective casings beyond repair. The disaster followed: commissioning of the pumping station was delayed by one month, the manufacturer reputation being badly damaged.
To avoid such situations, negotiating prices shall be slowed down to a pace once you cross the line of the target price - your conservative estimate based on the prices for similar pumps available in the company database, current tariffs of the manpower, and construction material prices.
Globally distributed manufacturing of pumps and their parts demands higher standards of the quality assurance (QA) from both the manufacturer and the client. In mega-projects this requirement merely triggers a paper waterfall: only the QA documentation package of the high-pressure pump includes more than 35 items!
The following QA points have price-and-time implications.
- manufacturing facilities and foundry location,
- manufacturing inspection and test plan,
- requested pump test procedures.
The bidder shall confirm in writing that the pump shall be tested at full speed at the manufacture test facilities. In my past some bidders were not pre-qualified because of inadequate capacity of the facilities.
Performance guarantees - absolute efficiencies and the efficiency degradation over time - are the most difficult part of the negotiations as mutually exclusive interests clash.
The pump suppliers try by all means to pull the rope of guarantees to their territory - test facilities equipped with high-precision instrumentation and fully complying with the design requirements for test facilities described in ANSI/HI standards.
On the other hand, the purchaser is more interested in the field efficiencies implicitly guaranteed to the client through the specific energy consumption per m3/h of the desalted water.
To resolve the interests clash, 3 levels of performance guarantee are used in practice.
Basic level
By mutual agreement guarantees are limited to the shop efficiencies only. It is quite sufficient when the company has ample good operating records of the same pump make in the past projects. As well it may be applied in cases where the margin between guaranteed energy consumption of desalination and the predicted one is more than 10%. The main advantage is savings on the instrumentation and piping design, smaller footprint of the pumping station.
Extended level
Field efficiencies measured during commissioning are included into guarantees. Generally, pump suppliers accept this level provided that the piping geometry, instrumentation, and the efficiency measurement procedure are to be submitted to the supplier for approval. The weak point here is that the supplier may request full compliance with the HI recommendations for the flow meter and pressure gauges location, which are never followed in practice. The accepted compromise is the efficiency values reduced by 0.2 - 0.5%.
Full scope
Field efficiency degradation rates are added. The efficiency monitoring shall be started with the measurement of reference efficiency which may not coincide with the shop efficiency. The upper limit of the efficiency drop is 0.25% per annum. After the wear ring replacement the efficiency should restore to the reference value.
Progressive payment
Payment terms are the last point of negotiations where the process engineer involvement may substantially improve chances of getting what is expected. Just compare the terms offered by the pump supplier and the client, summarized in Tables 5A and 5B.
Table 5A Pump supplier progressive payment terms example
% | Milestone |
---|---|
10 | downpayment, upon order receipt |
20 | upon submittal of outline drawing |
30 | upon receipt of casing castings at manufacture's works |
40 | upon notification of readiness for dispatch |
Table 5B Progressive payment terms offered by client
% | Milestone |
---|---|
10 | downpayment, upon approval of the following documents submitted by the supplier: 1. pump specification review, 2. time schedule, 3. inspection and test plan |
20 | upon approval of the following documents: 1. GA drawing 2. CS drawing 3. coupling drawing 4. mechanical seal drawing 5. performance curves and startup torques 6. rotodynamic analysis, 7. test procedure |
30 | upon approval of NDT inspection of casing castings and certificates of material compliance at foundry site |
35 | upon the pump test results approval and pump delivery ex-works |
5 | upon full document package delivery |
Michael Homer (ClydeUnion) wrote
There are just 2 points that I think would be worth adding.
- I refer to your paragraph where you state "There are no other methods of improving efficiencies than the impeller hydraulic passage optimisation and impeller surface polishing". I think it would also be worth mentioning here that the wear part clearance also affects efficiency. The smaller the clearance the lower the losses are over the components For this reason on RO pumps it has been our standard practice since the Trinidad pumps to use PEEK wear parts which are completely non galling and this enables us to reduce the wear ring clearances. This increases efficiency by 1% - 2%.
- Referring to your proof of experience explanation. I think it would also be worthwhile taking into consideration the experience of a heritage company no longer part of the same group but whose designs exist within the company. For example David Brown (now CLYDEUNION Pumps) has its heritage in Bingham and made pumps under licence to Bingham until Sulzer bought Bingham in the 1980's. As Sulzer (MSD) and David Brown (DB34) technical heritage is both from Bingham, Sulzer experience should also been take into consideration when qualifying David Brown as the pumps are from the same original source.