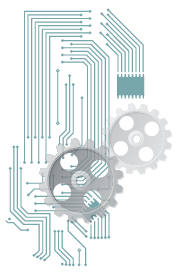
Design Thinking is the only instrument for creating Know-How.
It is a dominant methodology in business today. Unlike its predecessor - Problem Solving, it focuses on enriching the client's experience – not on acing in some specific field. The eye-catching difference between both may be illustrated by the problem of hanging a picture on the wall. The problem solver will focus her attention on making the best hole in the hardest concrete, while the design thinker starts by selecting the best place on the wall and lighting as a bad one may kill the picture and the client's experience as well.
Four out of five stages - Empathize, Define, Ideate, Prototype, and Test - of design thinking drill on systematic reasoning. It is deeply rooted in structured knowledge being churned out around the clock by Standardization & Unification (S&U).
S&U is fundamental and omnipresent; they form our demands and habits, behavior and responses, the ways we are taught at universities, and how we build businesses. Every big success or failure may be explained by S&U. For example, one may say that Amazon.com skyrockets because it learned how to fish S&U's recurring stable patterns out of the ocean of the customers' demands.
S&U is our language. Some years ago a tender for a desalination mega-project (over $100 million) was actually canceled just because the proposed technical solutions for the same set of the client's requirements were different – and could not be compared within the S&U framework adopted by the client. This framework failed in its basic task – to allow a measure of uniformity and homogeneity among the engineering solutions proposed by the bidders.
The modern paradox is that innovation – the diversification synonym - may flourish only in the context of a well-formed S&U system offering bricks and mortar for the ideas implementation. The deeper the S&U system, the more competitive and fast implementation is.
S&U fuels the business culture – the same one that “eats strategy for breakfast” (Peter Drucker) as S&U effectively depersonalizes and "objectifies" the ideas turning the business into a success.
I once worked for a company where a stable aversion to documenting S&U requirements was part of the culture. Recently this company has gone through nearly 65% downsizing. It is not difficult to deduce that the accompanying percentage loss of knowledge and expertise was of the same order. It would not have happened with the proper S&U framework in place as S&U fixes sustainable patterns making the business achievements irreversible and immune to the staff turnover. How high is it today? Judging by my email list changes it is about 20% per year (mostly engineering companies). It means that in 5 years a company may lose to its competitors without a proper S&U system.
Information S&U is imperative for digital transformation to succeed: it breaks barriers of data sharing, structuring, and prioritizing. Even the pace of the industrial Internet of Things (IIoT) propagation is measured by S&U. It's cool to say that data is the modern oil. Not all the data – only structured, tagged, and filtered by S&U.
One may object to my ode on S&U by saying that there are a few businesses built upon the revenue model leveraging bespoke products and services. These companies simply succeeded in discovering stable patterns in pseudo-diversification. They work at a different level of S&U – not physical components and parts, but abstractions implemented as software libraries and frameworks or generic algorithms like in 3D printing and CNC machining.
But the most amazing examples of S&U-driven diversification may be found in conventional engineering like process one where 95% of the project development is done by copy-scale technique. Physical scaling does not affect abstractions governing the first.
The prevailing reasoning that keeps engineering stuck in the rut of the copy-scale paradigm (and the core-business philosophy) is that its effect (shorter delivery, higher quality, lower costs, no learning curve) grows with the number of projects executed. It was true in the Problem Solving Age. Now these companies lose competition to Design Thinkers for good as the project contents change.
Deep down, it is standardization problems that separate the first group from the latter.
One of them may be illustrated on how to link the item on the Piping & Instrumentation Diagram (P&ID) to the product in the market. It is a problem of vague or fuzzy identities: an infinite number of P&ID items shall be served with a finite number of products undergoing perpetual evolution.
How does Crenger.com solve the problem of fuzzy identities?
It introduces standardized conditions grid and generic product (GP) abstractions.
The notion of a grid captures recurring design conditions (the same process pressures, temperatures, flow rates, and fluid quality). GP is a major building block for engineering services providers engaged in assembling the procured equipment pieces.
GP may be considered a common denominator of constantly evolving off-the-shelf products A, B, and C in the market. On the process side, it is applicable to a range of operating conditions or requirements as well. For example, the same metal piping of the ANSI class 150 may be used for a range of pressures from 0 to 22 Barg. Another example is the rating classes of the motor circuit breakers.
From a data processing perspective, GP is a unique set of stable attributes describing generic product functionality, design, and construction. These attributes are major price-formers as well. GP is a mediator between engineering demand on the one hand, and the market products diversity, on the other hand. GP acts across all projects and stores the design information gained in the past.
As a mediator, Crenger's GP is akin to Google’s Multilingual Machine Translation System. It uses some generic machine language allowing the translation of language pairs it has never seen before. For example, if the system has been trained to Japanese-English and Korean-English pairs, it produces good translations of Korean-Japanese pairs too.
Crenger auto-generates GP for Piping & Instrumentation Diagram (P&ID) items or selects the nearest ones from the database. Then Crenger tries to map GP to products in the market. Here fuzzy identities problem meets its twin – how to select the best match from a set of slightly non-conformant products? I plan to return to this amazing problem in my future post.
Standardization clears the way to Unification. By analogy with LEGO game, standardization is all about selecting parts, while unification is assembling these parts into something useful.
Unification is where expertise meets innovation: it creates endless consolidated abstractions kindling the design thinking.
A trivial example of engineering unification is P&ID composite symbols introduced by ISO14617. It was relegated to insignificance by all P&ID software providers failed to understand the criticality of information hiding principle of unification.
Hiding by unification reduces the P&ID perceptive complexity - a major hurdle in presenting P&D as the project roadmap, and a bottleneck of the functional requirements specification – the domain where unification reigns.
The same software providers failed the second time by ditching the recurring P&ID items group concept introduced by ANSI/ISA-S5.1 – a key to understanding how the process engineer thinks. In simpler terms, it says that no multiple copies of the same combination of P&ID items shall be shown on P&ID.
Unification laws dictate that Process Flow Diagram (PFD) and P&ID be contracted and expanded views of the same object. Ever thought of this? You will be surprised to know that Crenger already implemented all these three basic S&U requirements.
Like MS WORD, Crenger enhances the unification principle by introducing Copy, Paste, Scale, Autocomplete, and "Grammar check" algorithms for P&ID data. They boost the quality and speed of project execution by 10 - 100 times and let Artificial Intelligence (AI) into Engineering. Auto-completion means auto-sizing and auto-connecting the P&ID primary item and the secondary one (piping, instruments, fitting, valves) in a way established by good engineering practice.
Crenger actually designs parts of P&ID without a single direction from the user. For instance, it specifies the suction and discharge piping with drainage valves for a pump, sizes motors and variable speed drives, valves, and instrumentation. The depth of the data copying is selected by the user – it may include the control structures, documents, and drawings as well. The above-mentioned method features Bulk Update & Scaling – the copied subsystem may be “filled” with another fluid and scaled up or down by automatic re-sizing of its equipment and piping.