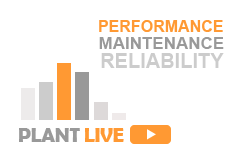
Generally Digital Twin is a virtual presentation of some physical asset. The same one may be represented by a number of DTs serving different purposes. Purpose defines the DT life cycle. For example, mechanical 3D model is used before the plant construction, the plant operation does not need it.
What makes DT meaningful? The ability to predict the outcome that cannot be obtained by other means, future or present. This requirement drives the DT development. Can you identify it in the following description?
The plant remote data acquisition system is not DT unless it is equipped with algorithms predicting the remaining useful life (RUL) of the asset, or the equipment abnormal conditions, or its failure times. These tasks are the essence of plant maintenance.
DT development is part of the business digitization. It makes or breaks DT. Both are endless in time, going deep into engineering fundamentals. Both require new know-how. It cannot be discovered by assembling DT from disparate IT tools available on the market (like BIM or SCADA or Siemens SIMIT).
New business paradigm
DT is a door to a new business paradigm. The company creates the catalog of customizable DTs. The customer selects DT and checks how it works. The company customizes and materializes DT.The smart customer questions are the same whether she buys a family car or a multi-million desalination plant.
- What maintenance shall be done and how often?
- How is it reliable?
- How economical is it?
The DT in question shows in real time (accelerated or not)
- the plant equipment state and performance parameters
- the plant maintenance tasks (like intake pigging, CIP cleaning, etc.)
- the equipment preventive maintenance tasks and tests to be executed
- the equipment failures
- total power consumption, production and energy cost
This DT is not built solely for a customer; it is extensively used for the plant design validation and optimization. In practice DT failure always leads to mismatch between the equipment pieces.
In the future it will serve as a basis for operation and maintenance personnel training – reason number one why many customers opt for more expensive PPP contracts.